pph管的擠出成型工藝流程方法介紹
Introduction of extrusion process of PPH pipe
pph管的擠出成型工藝流程方法介紹
Introduction of extrusion process of PPH pipe
1、原料的選擇:擠塑聚丙烯管材用樹脂,其熔體流動速率在0.2~0.3g/10min范圍內。一般熔體流動速率在0.2~0.4g/10min范圍內的樹脂應用較多。
1. Selection of raw materials: resin for extruded polypropylene pipe, its melt flow rate is in the range of 0.2-0.3g/10min. Generally, resins with melt flow rate in the range of 0.2-0.4g/10min are widely used.
2、聚丙烯管生產(chǎn)工藝順序:與通用型聚乙烯管的生產(chǎn)工藝順序相同,工藝順序如下。原料開袋檢查質量→擠出機把原料塑化熔融→模具成型管坯→真空定徑套冷卻定徑→真空噴淋冷卻→管材冷卻降溫→牽引→切割→檢驗質量→入庫。
2. Production process sequence of polypropylene pipe: the same as that of general polyethylene pipe, and the process sequence is as follows. Open the bag and check the quality of raw materials → the extruder plasticizes and melts the raw materials → the mold is formed into the tube blank → the vacuum sizing sleeve is cooled and calibrated → the vacuum spray is cooled → the tube is cooled and cooled → the traction is pulled → the cutting is performed → the quality is inspected → the product is put into storage.
3、設備的選擇:聚丙烯管材多采用通用型單螺桿擠出機生產(chǎn)成型。
3. Selection of equipment: polypropylene pipes are mostly produced and molded by general single screw extruder.
螺桿結構為等螺距不等深漸變型,長徑比為(25~30):1,壓縮比為2.5~4。成型模具結構多為直通式,芯棒定型平直部分長L=(2~5)D(D為管材的直徑,直徑小時取***值,管材直徑***時取小值)。定徑套的內徑d=D/(1-δ)(D為管材直徑,δ為管材收縮率,一般δ=2.7%~4.7%)。
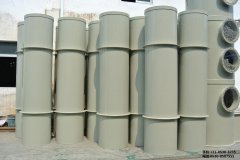
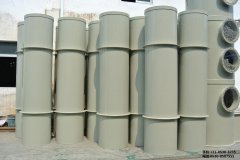
The structure of the screw is of constant pitch, unequal depth and gradual change, the ratio of length to diameter is (25-30): 1, and the compression ratio is 2.5-4. The structure of the forming die is mostly straight through type, the length of the flat part of the core bar is L = (2-5) d (D is the diameter of the pipe, the larger value is taken when the diameter is small, and the smaller value is taken when the pipe diameter is large). The inner diameter of the sizing sleeve is d = D / (1 - δ) (D is the pipe diameter, δ is the pipe shrinkage, generally δ = 2.7% - 4.7%).
4、管材擠出成型工藝溫度:機筒的加料段150~165℃,塑化段170~180℃,均化段190~220℃。成型模具溫度190~220℃。
4. Tube extrusion process temperature: feeding section 150-165 ℃, plasticizing section 170-180 ℃, homogenizing section 190-220 ℃. The mold temperature is 190-220 ℃.
5、PPH等塑料管材在生產(chǎn)過程有時會出現(xiàn)塑料化不***、焦燒,這是什么原因呢?
5. In the production process of PPH and other plastic pipes, poor plasticization and scorch sometimes occur. What's the reason?
一、焦燒
Coke burning
1、焦燒的現(xiàn)象
1. Scorch phenomenon
(1)溫度反映超高,或者是控制溫度的儀表失靈,造成塑料超高溫而焦燒。
(1) the temperature reflects the ultra-high temperature, or the instrument controlling the temperature is out of order, causing the plastic to scorch due to the ultra-high temperature.
(2)機頭的出膠口煙霧***,有強烈的刺激氣味,另外還有噼啪聲。
(2) there is a large smoke at the rubber outlet of the machine head, which has a strong pungent smell and crackling sound.
(3)塑料表面出現(xiàn)顆粒狀焦燒物。
(3) granular scorched substance appears on the plastic surface.
(4)合膠縫處有連續(xù)氣孔。
(4) there are continuous air holes at the joint.
2、產(chǎn)生焦燒的原因
2. Causes of scorch
(1)溫度控制超高造成塑料焦燒。
(1) plastic scorch caused by over high temperature control.
(2)螺桿長期使用而沒有清洗,焦燒物積存,隨塑料擠出。
(2) if the screw is used for a long time without cleaning, the scorched material will be accumulated and extruded with the plastic.
(3)加溫時間太長,塑料積存物長期加溫,使塑料老化變質而焦燒。
(3) if the heating time is too long, the plastic deposit will be heated for a long time, so that the plastic will age and deteriorate and burn.
(4)停車時間過長,沒有清洗機頭和螺桿,造成塑料分解焦燒。
(4) the parking time is too long, the machine head and screw are not cleaned, resulting in the decomposition and burning of plastic.
(5)多次換?;驌Q色,造成塑料分解焦燒。
(5) mold change or color change for many times, resulting in decomposition and burning of plastic.
(6)機頭壓蓋沒有壓緊,塑料在里面老化分解。
(6) the head gland is not pressed tightly, and the plastic is aged and decomposed inside.
(7)控制溫度的儀表失靈,造成超高溫后焦燒。
(7) the temperature control instrument fails, resulting in scorch after ultra-high temperature.
3、排除焦燒的方法
3. Method of eliminating scorch
(1)經(jīng)常的檢查加溫系統(tǒng)是否正常。
(1) regularly check whether the heating system is normal.
(2)定期地清洗螺桿或機頭,要徹底清洗干凈。
(2) clean the screw or head regularly and thoroughly.
(3)按工藝規(guī)定要求加溫,加溫時間不宜過長,如果加溫系統(tǒng)有問題要及時找有關人員解決。
(3) according to the requirements of the process, the heating time should not be too long. If there is a problem in the heating system, it should be solved by relevant personnel in time.
(4)換?;驌Q色要及時、干凈,防止雜色或存膠焦燒。
(4) mould change or color change shall be timely and clean to prevent mottled or burnt glue.
(5)調整***模具后要把模套壓蓋壓緊,防止進膠。
(5) after the mold is adjusted, the mold sleeve gland shall be pressed tightly to prevent the glue from entering.
(6)發(fā)現(xiàn)焦燒應立即清理機頭和螺桿。
(6) clean the head and screw immediately in case of scorching.
二、塑化不***
II. Poor plasticization
1、塑化不***地現(xiàn)象
1. Poor plasticization
(1)塑料層表面有蛤蟆皮式地現(xiàn)象。
(1) there is toad like ground on the surface of plastic layer.
(2)溫度控制較低,儀表指針反映溫度低,實際測量溫度也低。
(2) the temperature control is low, the temperature reflected by the instrument pointer is low, and the actual measured temperature is also low.
(3)塑料表面發(fā)烏,并有微小裂紋或沒有塑化***地小顆粒。
(3) the plastic surface is black, and there are tiny cracks or small particles without good plasticization.
(4)塑料的合膠縫合的不***,有一條明顯的痕跡。
(4) the gluing of the plastic is not well sewn and there is an obvious trace.
2、塑化不***產(chǎn)生的原因
2. Causes of poor plasticization
(1)溫度控制過低或控制的不合適。
(1) the temperature control is too low or improper.
(2)塑料中有難塑化的樹脂顆粒。
(2) there are resin particles that are difficult to be plasticized in plastics.
(3)操作方法不當,螺桿和牽引速度太快,塑料沒有完全達到塑化。
(3) the operation method is improper, the screw and traction speed are too fast, and the plastic is not fully plasticized.
(4)造粒時塑料混合不均勻或塑料本身存在質量問題。
(4) uneven mixing of plastics or quality problems of plastics during granulation.